|
|
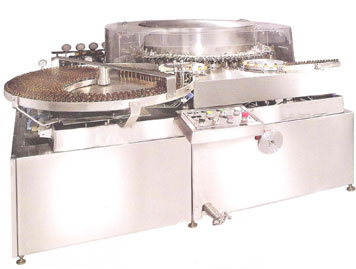 |
INTERTECH offers customized plant construction for the pharmaceutical injectable industry demand of Washing, Sterilizing , Filling & Closing line. A set of machineries are synchronized for the processing of vials. Compact installations are particularly economical and flexible in respect of format and product change over. The space saving and energy saving compact installation are clearly laid out and easy to operate with saving in number of operators, less personnel movement in the classified area. The equipment specification conform to quality guidelines GAMP4 and supports 21 CFR PART 11 requirements.
|
|
|
|
We offer following Compact Sterile DrY Powder Vials Processing Line:
Dry Powder Vial Compact line |
300 |
Dry Powder Vial Compact line |
200 |
Dry Powder Vial Compact line |
150 |
The entire line consists of linkage of Vertical Washing Machine, Sterilization Tunnel & Filling and Closing Machine. All linkage accessories along with filtration skid for water, Laminar Air Flow are also supplied along with complete line.
|
VIAL WASHING MACHINE
Vials Washing Process: |
Vials Working Description: |
- Ultrasonic treatment (optional)
- Recycled water (internal and external)
- Compressed air (internal)
- Purified water (internal)
- Compressed air (internal)
- WF1 (internal)
- Compressed air (internal)
|
Vials can be fed on to an in feed conveyor or alternatively a turntable from where they are fed to a star-wheel and delivered to a revolving conveying system consisting of 40 or 60 grippers equally spaced. V-grippers are mounted o the circumference of the gripper ring, which rotates around a vertical axis. The horizontal rotation of the vial through 180˚ during the in feed as well as the opening and closing of the grippers is cam-controlled. Vials are passed through the cleaning station upside down. At the individual stations, spray tubes travel is synchronized with vials, then enter the vials whose orifices are exactly centered. The spray tubes follow the continuously moving grippers from the start to the finish of a working station and retract. |
|
Max diameter
Nos./min |
Max height |
Capacity |
Grippers |
Vials sizes |
25 |
45 |
300 |
60 |
38 |
61 |
200 |
60 |
25 |
45 |
200 |
40 |
53 |
97 |
120 |
40 |
25 |
60 |
120 |
26 |
44 |
73 |
80 |
26 |
|
|
SALIENT FEATURES
- All parts that come in contact with the internal surface of the ampoule/ vial and wash media are made of AISI SS 316L stainless steel.
- Other parts are made from engineering plastics, FDA approved or AISI SS 304 stainless steel.
- The washing process can be customized to your requirement. Each vial or ampoule is guided through a series of process steps.
- Short set up time, fast & simple size change ensures versatility of use for different ampoule/vial
- All electronically controlled features of machine can be equipped through PLC with operational data logging system for the documentation of all data relevant to the production
VIAL STERILIZATION & DE-PYROGENTAION TUNNEL
De-pyrogenation tunnels designed to sterilize and de-pyrogenate glass containers with a continuous process maintaining an ISO 5 environment along the whole length and width of the conveyor belt complying with ISO 14644-1 requirements.
Designed to allow higher outputs in a more compact body and with better control of the process. INTERTECH tunnels are equipped with
- Cooling system for the cooling zone.
- Sterilizing of the cooling zone.
- Automatic air balancing between aseptic and non-aseptic area of the tunnel.
- Shutter positioning monitoring and automatic adjustment are some of the options available to meet specific customer requirements.
TECHNICAL PARAMETERS
- Sterilizing Temperature – 350 Deg C
- Sterilizing Time – 5min to 7 min
- Net stripe speed – 50-250 mm/min
- Cleanness grade & method – 100 class with vertical laminar flow
- Speed – 100 to 300 Ampoules /min.
Technical Specifications |
|
DST 300 |
DST 400 |
DST 450 |
DST 600 |
DST 900 |
DST 1200 |
Length |
2700 |
3315 |
2800 |
2800 |
3900 |
4200 |
Height |
2400 |
2400 |
2400 |
2400 |
2400 |
2400 |
Width |
1300 |
1400 |
1400 |
1450 |
1550 |
2150 |
Belt width |
300 |
400 |
400 |
450 |
600 |
1200 |
Exhaust Air-m3/hr |
1347 |
1845 |
1845 |
1244 |
4448 |
8227 |
Installed Power(kw) |
38 |
45 |
45 |
29 |
55 |
95 |
SALIENT FEATURES
- Each independent filter plenum is provided with filter integrity sample ports.
- The equipment’s conveyor net is monitored and alarm status is activated if it operates outside the belt speed set points.
- Provision for ports to allow introduction of validation thermocouples in each zone
- The tunnel is provided with fully integrated vial flow control logic to allow automatic stops and restarts of the equipment.
- All filter modules have differential pressure gauges to monitor pressure. Pressure switches with high and low alarms
- When the tunnel is not in use it can be operated in night-mode to save energy while preventing contamination.
- The air quantity in whole machine can be set to auto section frequency- conversion balance.
- All critical parameters i.e. temp., Fan speed etc. has auto recording facility.
LIQUID VIAL FILLING, STOPPERING & CLOSING MACHINE
VIALS FILLING & STOPPERING MACHINE MONO BLOCK DESIGN
|
|
|
All Parts in contact with filling media are of SS316 L AISI 316L material A turntable and a one to two lane in feed belt feed the vials into the conveying system. The machine comprises two parts, filling and stoppering . It can automatically finish a series of procedures, i.e. Vial feeding, filling (additional nitrogen blanketing) & stoppering. No bottles no filling. Also it has overloading protection and malfunction alarm functions. Imported peristaltic pump, gravity valve volume-metering pump and rotary valve volume meter pump are available options.
FEATURES
- Volumetric dosing – pump & pinch valve & with 2 part seal less rotary valve system
- Optional metering device, peristaltic pump and piston pump, with adjustable filling volume.
- Stoppers are conveyed by double vibrators in double tracks and bottles are capped with double heads.
- High filling accuracy without drips and drops.
- No vial no filling, no stoppers no capping.
- Optional dustproof cover and class 100 laminar flow safeguard device according to customers requirements.
- Nitrogen flushing before & after filling
- Lyophilizer collector tray at the out feed.
- Vial sampling after closing with stopper
- Torque limited for in feed & out feed turre
Technical Specifications |
Capacity |
80 ~ 300 Vials /Min |
Volume of Vial |
1 ~ 20ml |
Accuracy |
peristaltic pump: ±0.5%; piston pump: ±1% |
Power supply |
380V 50Hz |
Power |
1.2Kw |
Compressed air consumption |
10 ~ 15m3∕h |
Dimensions |
2100× 1750× 1400mm |
STOPPERING STATION
To minimize the risks of particles, the rubber stoppers are picked-up by vacuum from a vertical plane away from the containers and with a rocker arm plunger, placed onto the vial. This system operates by vacuum / compressed air principle. The system processes an extraordinarily broad spectrum of powders, dust free and with great precision, owing to the very small and easily manageable design changeover.
Technical Specifications |
Technical data |
IET 150 |
IET 300 |
IET 200 |
Output |
150/min (4 head) |
300/min (8 head) |
200 / min (6 head) |
Vial dimensions |
D=16-70 mm, H=35-180 mm |
D=16-52 mm, H=35-105 mm |
D=16-86 mm, H=35-140 mm |
Min dosage |
1ml to 30 ml |
|
|
|
WORKING PRINCIPLE
Leading edge technology in compliance with cGMP design criteria. Perfect understanding of the needs of our customer, blossoms in to a product of high quality and performance from engineering and manufacturing to commissioning at customer plants.The time tested principle based on individual self rotating rollers that pivot into each container rim thus creating a low particle high quality seal. Operation of the machine is easy and simple. Accessibility for cleaning and maintenance is excellent.. Size changeover is fast, easy and reproducible with the help of digital position indicators.
CHECK DEVICE
- Containers detection of the in feed
- No stoppers – no cap
- Low level cap feed
- Serial fault monitoring display
- Torque limiter for in feed and out feed turret
OPERATION
Bunged vials are fed by a turntable or a conveyor to the in-feed slotted wheel. The in-feed wheel feeds the spaced vials to the sealing turret. Simultaneously to this action the vial collects a cap each from the end of a cap feed chute and imparts it in a proper orientation for the sealing. The sealing turret consists of eight sealing heads which are identical. These eight sealing heads skirt, spin and seal the cap onto the neck of the vial.
TECHNICAL DETAILS
|
Diameter |
Height |
Capacity |
IET 4 |
16-86 mm |
35-180 mm |
150 (for smallest range) |
IET 8 |
16-52 mm |
35- 105 mm |
300 (for smallest range) |
IET 6 |
16- 70 mm |
35-140 mm |
200 9for smallest range) |
Vial Sizes |
D 14.5 mm to 80mm |
Cap sizes |
H 13.20 mm to 30 mm |
Output Speed |
100 to 300 Vials/min |
Voltage |
200 V, AC Supply for vibrator
415 / 380 V, 50 Hz, 3 Phase
AC Supply for machine |
Main drive |
1.5 HP |
Dimension |
955x1015x1700 (LxWxH) |
|
|